Background
With the accelerated advancement of new industries, the requirements for accuracy, efficiency, and stability in the manufacturing industry are becoming increasingly demanding. It is difficult to rely solely on mechanical technology to improve the precision and performance of machine tools. And it is no longer able to meet production needs. Automated machine tools have emerged as an important means of realizing the transformation and upgrading of manufacturing industries.

To meet the transformation needs of the 5G era machine tool industry, Bivocom has independently developed a 5G automated machine tool solution. With the advantages of high speed, massive connection, low latency, and high reliability of 5G technology, various types of production equipment, controllers, etc. are interconnected. In addition, the solution also uses PLC technology, IoT technology, etc. to achieve functions such as data collection, equipment control, remote operation and maintenance, and production capacity monitoring, thereby improving production efficiency and quality, and reducing labor costs and resource waste.
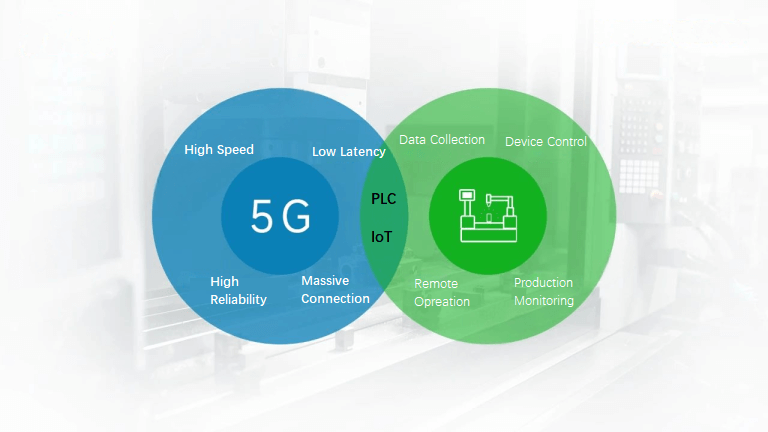
Pain Point Analysis
- The machine tool equipment relies on manual operation, which makes the production process relatively cumbersome, slow, and prone to errors. It requires a lot of manpower and time input, resulting in low production efficiency.
- There is a lack of data analysis capabilities, which means that adjustments and optimizations can only be made through manual experience and observation.
- Traditional machine tools can only finish processing tasks of specific shapes, sizes, and materials. It is poor flexible that cannot adapt to multiple product types and changes.
- When the machine tool equipment malfunctions, maintenance personnel are unable to remotely operate and guide the machining, resulting in serious production losses.
System Solution
To address the low productivity, inflexibility, and low degree of automation of traditional machine tools, the Calculus IoT 5G automation machine tool application solution combines new technologies such as automatic control, 5G, the Internet of Things, and sensing. It uses the 5G industrial gateway TG463. It connects with various types of sensors installed on the automated machine tool, such as temperature sensors, voltage sensors, pressure sensors, speed sensors, displacement sensors, and laser sensors. This allows for remote monitoring of the operating status of the motion axis, cutting tools, and other mechanical or electrical components inside the machine bed in real time. And the system also collects information such as the temperature, vibration, and sound of the CNC machine tool, converts the monitored data into digital signals, and records and monitors the machine tool’s operating status in real-time based on the different status information. The information data is then transmitted to the Bivocom monitoring platform via the communication function of the 5G private network. When the production equipment completes its production tasks, the monitoring platform can update the task status in real-time, enabling management personnel to keep abreast of production progress and quality.

Furthermore, with the help of industrial big data technology, monitoring platform can also perform statistical analysis and predictive maintenance on the collected data, timely identify potential safety hazards, equipment failures, etc., and nip the hidden dangers in the bud.
Solution Functions
Remote Management and Control
Management personnel can remotely monitor the operation status and equipment failure rates of the machine tool and PLC in real time through APP, PC, etc. In the meantime, remote program issuance, machine tool program query, machine tool processing trajectory adjustment, automatic program content feedback, and other functions are supported.
5G Private Network
Leveraging the technological capabilities of 5G’s massive connectivity, production equipment can be automatically collected, transmitted in real-time, and locally stored at a sub-second level. This enables automation and intelligence of the production process, improving efficiency and product quality, and ultimately achieving greater commercial value and competitive advantage.
Production Capability Monitoring
Analyze data through various sensors and monitoring devices, and monitor and record the production process of CNC machine tools in real-time, thereby analyzing and evaluating their production capacity and efficiency, achieving more precise production and higher product quality.
Remote Programming
Building a VPN network maintenance channel enables remote engineers to perform operations such as program downloading and programming debugging online, saving time and cost investment, and improving equipment maintenance efficiency.
Value of Solution
-
Automation
With the help of artificial intelligence algorithms, it can realize the automatic scheduling and optimization of production lines, improve the utilization and efficiency of production lines, and enhance company competitiveness and market share.
-
High Flexibility
By rapidly responding to market demands and customized customer requirements, it is possible to achieve flexibility and personalization in the production process, thus better meeting market needs.
-
Environmental Protection and Energy Conservation
Automated and intelligent production can achieve optimized energy utilization, and reduce waste emissions and environmental pollution, thus achieving environmental protection goals.
Comment